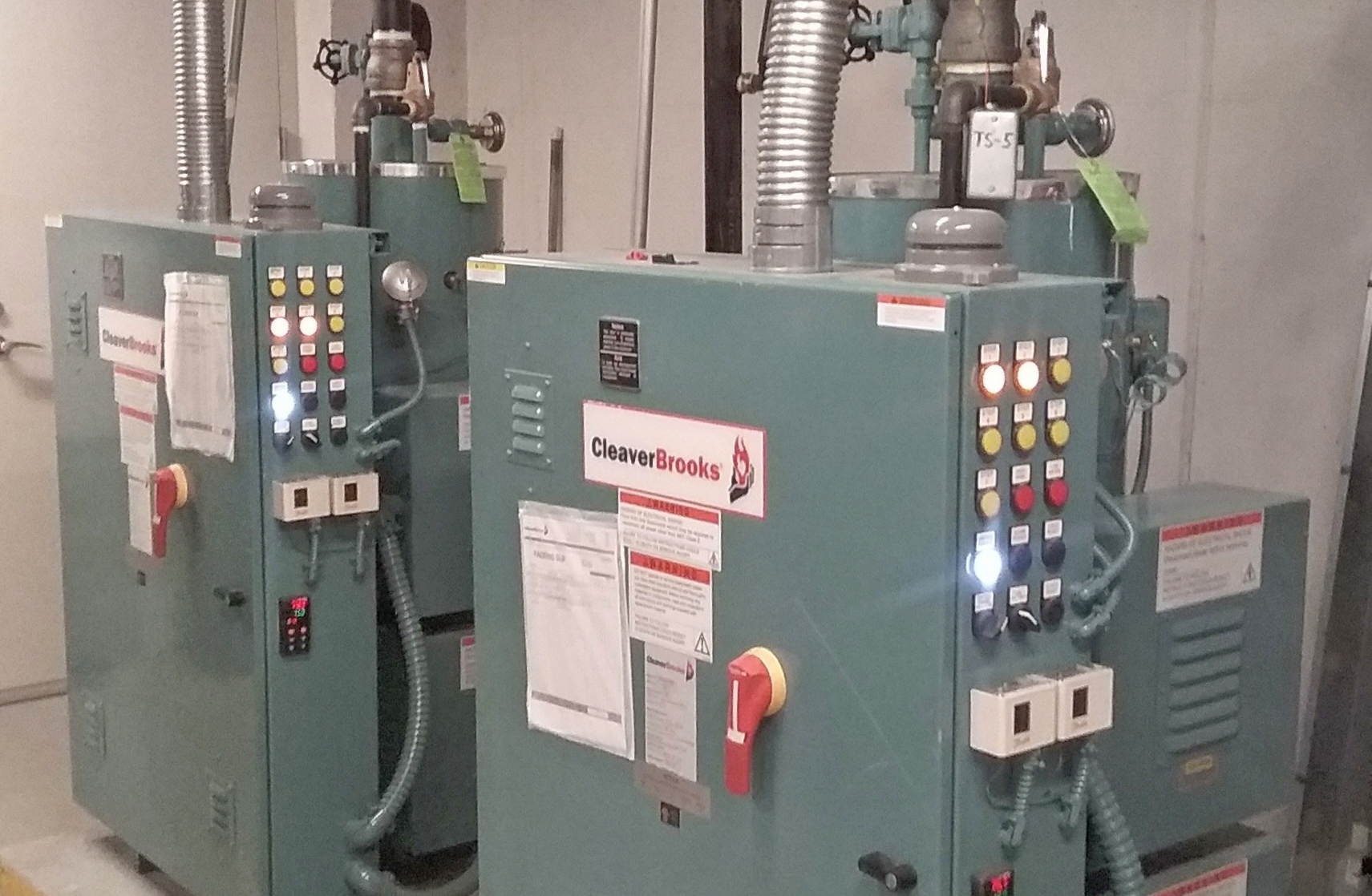
Reducing your Carbon Footprint with Electric Boilers
June 7, 2022Routine boiler tuning is essential for maintaining maximum combustion efficiency, reliability, and safety. Combustion efficiency measures how effectively fuel’s heat content is converted to usable heat. Tuning the burner during the spring and fall is recommended due to significant changes in air temperature and density during these seasons.
Both steam and hot water boilers require regular tuning. It is crucial to tune a boiler when it is hot, as a cold boiler can distort actual operating O2 and CO readings.
Steps for Tuning a Natural Gas-Fired Boiler
- Preparation:
- Ensure the boiler is warm, has a load, and shows a zero pressure reading on the steam gauge.
- Insert the probe into the stack to monitor stack temperature, O2, and CO readings.
- Initial Setup:
- Power the burner switch and place it in manual mode at the low-fire point. The Burner Management System (Programmer) will control the burner, initiating pre-purging and ignition.
- Low-Fire Adjustment:
- Check the O2 analyzer for O2 and CO readings. If CO levels exceed 50-100 parts per million, the burner is running rich. Adjust the fuel or air accordingly. Aim for 5-8% O2 excess air at low fire.
- Check the manifold pressure at the burner entrance to ensure it is within manufacturer parameters.
- Incremental Firing Rate Increase:
- Manually increase the firing rate, observing the flame for signs of sooting or instability.
- Monitor the analyzer at each control point, adjusting cams and linkages to optimize the fuel/air ratio while maintaining safe firing conditions. Aim for 3% O2 or 15% excess air from medium to high fire with no more than 50 PPM of CO.
- High-Fire Adjustment:
- Focus on maximizing efficiency at the boiler’s most frequent firing rate, maintaining a safe excess air margin.
- Check manifold pressure at high fire to ensure full input as defined by the manufacturer.
- Return to Low-Fire:
- Manually reduce the burner to low fire, checking combustion readings and making minor adjustments.
- Observe linkage movement on single-point positioning systems for hitches or slippage. Switch from manual to automatic control, allowing the burner to modulate independently.
- Stability Check:
- Ensure the burner matches the load. Monitor boiler pressure relative to stack temperature. A well-tuned boiler should have a stack temperature 50-100 degrees above water saturation temperature. Higher temperatures may indicate a dirty boiler, flue gas bypass issues, or scaling.
- Safety Check:
- Test safeties, especially the low-water cutoff, auxiliary low-water cutoff, and flame scanner.
Conclusion
An out-of-tune boiler increases operating costs as energy is wasted through the stack. Soot buildup can cause tubes to overheat and crack or break, leading to extensive downtime and costly repairs. Regular tuning by a trained technician reduces energy costs and maintains optimal combustion.
By following these steps, you can ensure your boiler operates efficiently and safely, minimizing downtime and maximizing savings.