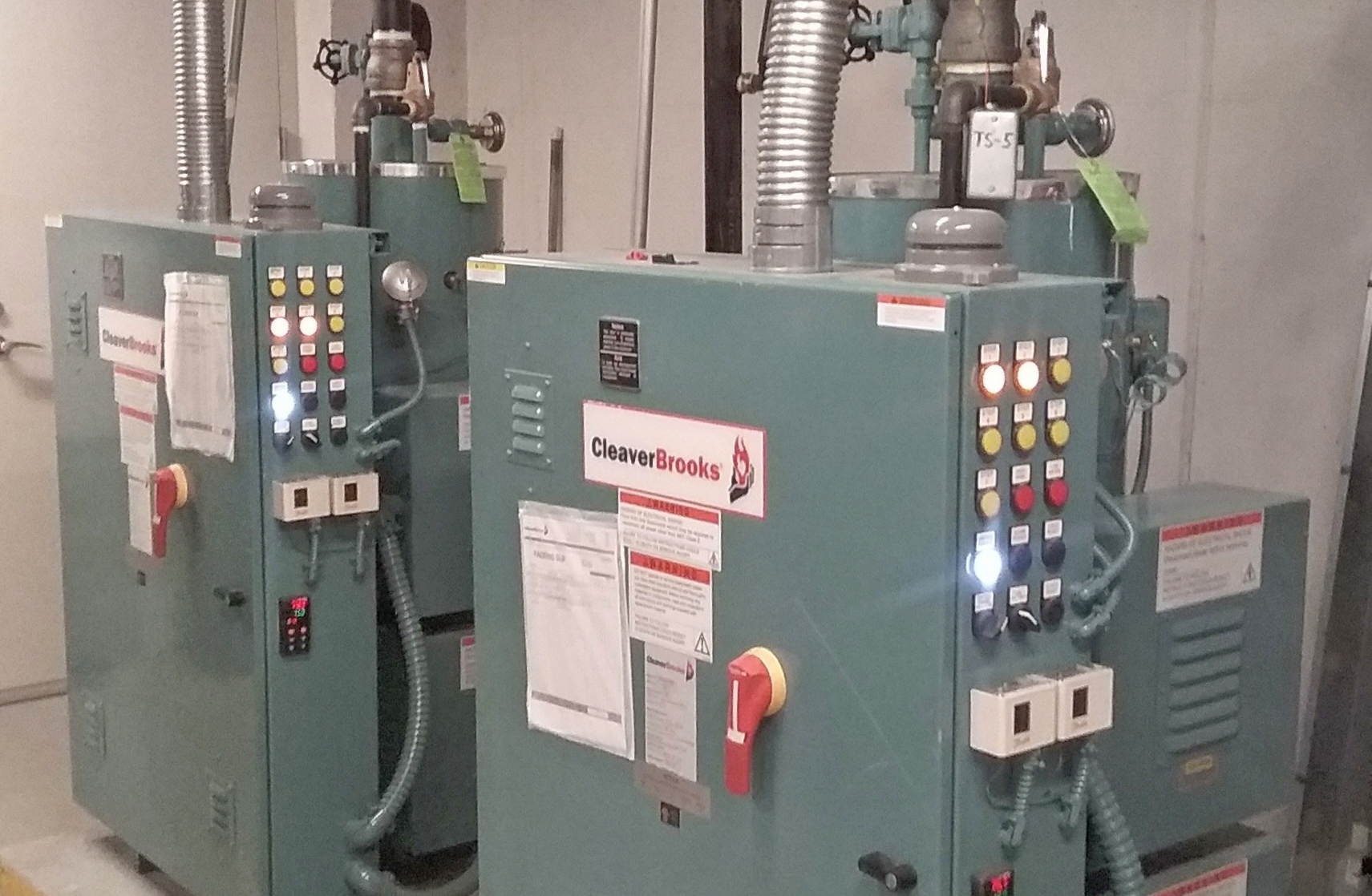
Reducing your Carbon Footprint with Electric Boilers
June 7, 2022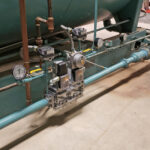
Upgrade Your Boiler’s Gas Train for Enhanced Safety & Efficiency
June 4, 2024With regular maintenance, a boiler can last 20 years or more, but it is likely operating well below its nominal efficiency of 80 percent. If the boiler pressure vessel is in good shape, consider upgrading the system to increase its efficiency and reduce ongoing operating costs. New developments in boiler controls and burners can enhance performance and produce measurable efficiency gains, resulting in annual cost savings. Here are a few options to consider:
Fuel-Air Ratio Control
Many boiler burners are controlled by a single-modulating motor with a single jackshaft that has connected linkages/arms to the fuel valve and air damper. Over time, these linkages tend to wear, stretch, and loosen, causing the fuel-to-air ratio to drift into either very inefficient excess-air conditions or unsafe fuel-rich conditions, which are also inefficient due to the heat transfer limitations caused by soot fouling.
To alleviate this problem, consider incorporating parallel positioning into the control system, replacing the single-jackshaft system. This control scheme uses dedicated motorized actuators for the fuel and air valves, electrically tying them into the electronic firing-rate control on the boiler. Burners that incorporate parallel positioning can eliminate this unwanted and inefficient shift from the optimum fuel-to-air ratio, consistently keeping the burner in sync as it modulates between low and high fire. Fuel savings of two to five percent are not uncommon with boilers that modulate considerably during a given operational day.
Oxygen Trim
Another way to ensure peak efficiency is to use an oxygen trim sensor/transmitter in the exhaust gas stream. The sensor/transmitter continuously senses oxygen content and provides a signal to the controller that “trims” the air damper or fuel valve, maintaining a consistent oxygen concentration when environmental conditions such as ambient temperature, relative humidity, and barometric pressure change. This system minimizes excess air while optimizing the fuel-to-air ratio and helps prevent the burner from going excessively rich, which is both inefficient and dangerous. It should be noted that a two-percent increase in oxygen over the optimum set point causes a one-percent loss in efficiency.
Variable Speed Drive
Adding a variable-speed drive (VSD) enables a motor to operate only at the speed needed at a given moment, rather than at a constant RPM regardless of load demand. This speed variance results in the elimination of unnecessary electrical energy consumption, as power consumption decreases significantly as speed lowers. A VSD can be used on any motor but is commonly found on boiler feed and circulating pumps and combustion air motors of more than 5 HP. These drives also offer quieter operation and softer starts compared to standard motors, reducing maintenance costs by decreasing stress on the motor shaft and associated bearings.
Lead-Lag Control
Incorporating lead-lag control of multiple boilers that are incrementally sized for the load can substantially reduce energy costs by reducing boiler cycling. Every time a boiler cycles off, it goes through a pre-and post-purging cycle before reigniting, during which ambient air blows through and across the heating surfaces of the boiler for approximately two minutes, purging valuable BTUs into the atmosphere.
Advanced Controls
Often called SCADA (supervisory control and data acquisition) systems, advanced control systems are PLC-based platforms that incorporate burner management, combustion control, and monitoring in one integrated package. By installing an advanced control system, a facility can expect better performance, enhanced safety, lower maintenance, and reduced operating costs. A key benefit of an advanced control system is that a boiler can be remotely monitored and managed within its safety parameters while simultaneously gathering and trending valuable information relating to safety, energy consumption, and maintenance trigger points. Operators can monitor boiler status via email, text messaging, voice mail, the Internet, or an internal communication system. In the event of a boiler-system alarm or malfunction, the control system can automatically alert an operator in a nearby or remote location.
High-Efficiency Burners
Upgrading the burner after about 20 years of service is strongly recommended due to advances in burner technology. Today’s burners are designed for high efficiency, high turndown, and low emissions. Increasing the burner turndown rate will increase energy savings because on-off cycles are reduced. Often, high-turndown burners can work in conjunction with a multiple-boiler lead-lag control system, delivering even more energy savings by further reducing cycling. Remember, even with the latest technology, regular maintenance is still necessary.